Carbon Fiber Reinforced Plastic (CFRP) Filaments used in most of FDM 3D Printer consist of randomly oriented carbon fibers embedded in a plastics matrix. By controlling and tailoring the orientation of carbon fibers, we are able to create
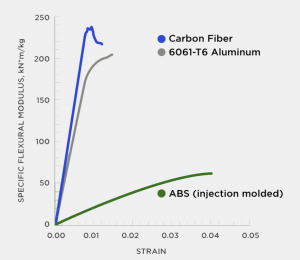
parts which are practically 30 times stronger than ABS, and also stronger than many metals we know.
Tensile Strength (MPa), Aluminum: 50 MPa, CFRP: 700 MPa
Tensile Modulus (GPa), Aluminum 70GPa, CFRP: 50GPa
Why most of 3D printed parts are not strong enough?
In a our recent paper published in IEEE, Sub-modeling Finite Element Analysis of 3D printed structures (http://dx.doi.org/10.1109/EuroSimE.2015.7103095 ), we have described that the main reason is due to the existence of intrinsic void and holes which are fabricated during the 3D printing process. In a Filament Fused Fabrication (Fused Deposition modeling) process, even when the users try to 3D print parts with 100% infill, they usually come up with 5% voids and holes distributed between the 3D printed layers. Upon applying an external force, the local stresses in the vicinity of the voids are much larger than the nominal stress or average stress theoretically calculated. The ratio of maximum stress to the average normal stress is knows as stress intensity factor. Our simulation results which are based on Finite Element Analysis and Sub modeling approach shows that in 3D printing FDM/FFF process, the stress intensity factor is 3.5. This means that the material strength is effectively reduced by factor of 3.5.
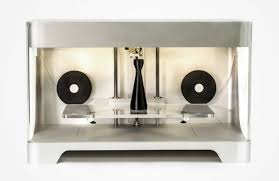
Application area of 3D Printed CFRP
Almost all of the Aluminum parts which were previously used to be fabricated using CNC, can now be 3D printed using CFRP. However 3D printing process additionally offer fabricating very complex shapes which are not possible using CNC. The cost of the machining is however cheaper and materials and weight of parts are much lighter as well. Therefore it offers wide range of applications in industry, robotic systems, medicine, etc.
How much does it cost?
Well, if you have a good idea for collaboration, then we will do it for you – for free.